丰田向特斯拉学习引入一体化压铸工艺,降低成本、简化工序
最近,丰田汽车宣布将在其即将推出的电动汽车上采用压铸技术(Giga-Casting)。类似于特斯拉的一体化压铸技术,丰田将汽车车身分为三个主要铸件——前部、中部(搭载电池组)、后部,从而实现 ” 重要部件集成 “。这不仅有助于简化工序,而且能够降低车辆开发成本与工厂投资。丰田表示,目标是在2026年时将开发费用减少至70%,未来降至50%;并且工厂投资在2026年将下降至50%。
丰田还展示了首个铸件,并将其与旧款零部件进行对比。值得注意的是,同样一个部位,旧款中至少包含数十个不同的零部件,而新款铸件仅有一大块金属。
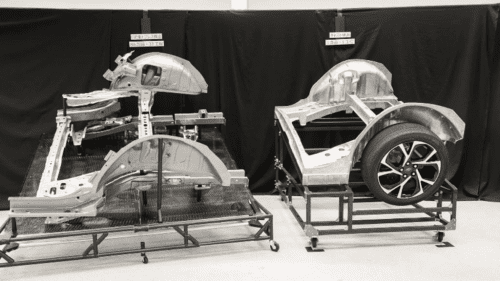
此外,丰田还计划建设一条 ” 自动推进式 ” 组装生产线。在制造过程中,这些正在生产中的车辆会 ” 自己向前开 ” ,完成工序。丰田曾表示,将从特斯拉的制造工艺中汲取灵感,并应用一体化压铸技术。
尽管追随特斯拉加入一体化压铸队伍的多是蔚来、小鹏、理想等一众新能源车企,但传统车企如通用汽车、现代汽车、沃尔沃汽车等也开始谋划采用这一技术。
汽车自重对碳排放总量有巨大影响。因此,汽车轻量化是解决节能环保与市场需求空间的矛盾关键。值得一提的是,一体化压铸能有效降低汽车的重量,从而达到降低油耗、提高续航里程的效果。
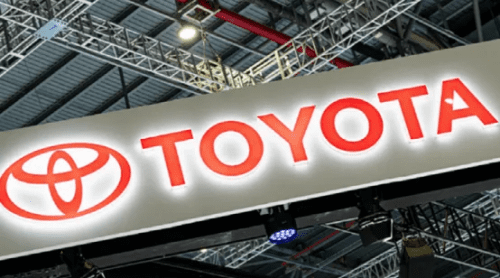
分析师们预计,一体化压铸零部件将逐步实现量产。随着整体行业降本增效需求爆发,或许会加速一体化压铸渗透率爆发,使新能源汽车2026年的一体化压铸规模超过300亿元。
总的来说,丰田在一体化压铸技术方面的探索表明,这一技术已经受到了越来越多的车企的重视,未来其应用前景广阔。